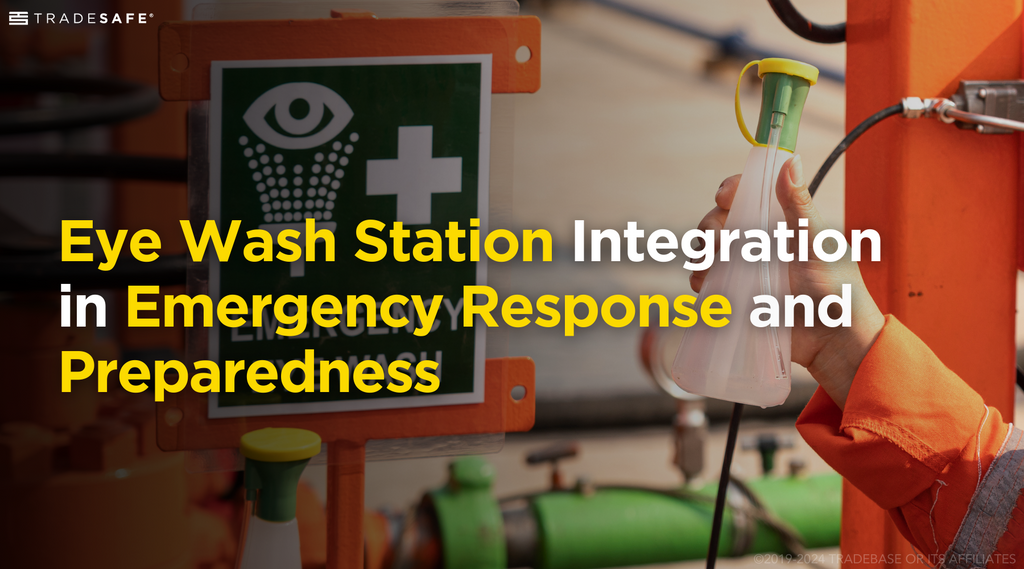
Natural disasters and emergency situations can unleash unpredictable hazards that can pose serious risks to safety and health, particularly to the eyes. Whether it's the debris from a tornado, chemical spills during an industrial accident, or the dust and ash from wildfires, the potential for eye injuries in such scenarios is high. In the chaos that follows a disaster, the eyes are especially vulnerable to irritation, physical trauma, or chemical burns, each of which can have devastating consequences on vision if not addressed promptly. This underlines the critical importance of emergency response preparedness, ensuring that immediate and effective measures are in place to protect against and mitigate such injuries.
Among the most vital components of this preparedness is the availability and accessibility of emergency eye wash stations. These stations play a pivotal role in the immediate aftermath of exposure to harmful substances, providing a swift means to flush out irritants and foreign materials from the eyes. The quick use of these stations can be the difference between a minor injury and severe, long-lasting damage.
Eye Exposure and Injuries During Emergency Response and Preparedness Efforts
Reports record that more than 18,000 workers experience eye-related injuries, particularly in occupations in the construction, production, and manufacturing industries. But outside of that, emergencies and natural disasters can create chaotic environments fraught with hazards, especially to the eyes. During such events, the risk of eye injuries escalates due to the presence of airborne debris, chemical spills, and other unpredictable factors. Eye injuries in these situations can range from minor irritations to severe trauma, potentially leading to permanent vision loss if not promptly and properly addressed.
Protecting the eyes in emergency situations is critical due to the high incidence of eye-related injuries reported during such events. Rapid response measures, including the immediate use of emergency eye wash stations, are vital. These stations provide the first line of defense in flushing out harmful substances and materials from the eyes, significantly reducing the risk of long-term damage.
To provide more context, here’s a closer look at the most common eye injuries and their causes:
- Chemical Burns: Often caused by accidental exposure to household or industrial chemicals, which become airborne or are mishandled during the emergency. The severity of a chemical burn depends on the chemical involved and how quickly the substance is washed out. Immediate dilution and flushing with clean water or a saline solution are crucial to mitigating damage.
- Scratches: These are caused by contact with dust, metal shavings, wood splinters, or even paper. Scratches can also occur from rubbing the eyes with dirty hands, which can introduce dirt or debris. While less severe than chemical burns, they can cause significant discomfort and sometimes lead to infections if not properly addressed. Flushing the eyes at an eye wash station can help remove particles that might cause or exacerbate abrasions.
- Impact Injuries: Objects like glass, wood, or metal fragments can become embedded in the eye during disasters like tornadoes, hurricanes, or explosions, leading to cuts, bruises, or punctures. Immediate washing of the eyes can help clear out any residual small particles that might cause further irritation or damage.
- Infectious Material: Exposure to harmful bacteria, viruses, or fungi can cause infections. Symptoms might include redness, pain, discharge, and blurred vision. Eye wash stations can help flush out these infectious agents quickly before they settle in and start causing problems.
- Thermal Burns: Exposure to steam or splashes from hot liquids can cause thermal burns to the eyes. Promptly rinsing the eyes with cool water from an eye wash station can help alleviate pain and reduce tissue damage.
- Ultraviolet Radiation Exposure: Natural disasters that disrupt electrical infrastructure can lead to inappropriate use of alternative light sources like welding equipment or ultraviolet lamps, exposing eyes to harmful UV rays. Quick and thorough eye washing can reduce the risk of complications such as infections or prolonged recovery times.
What Is An Emergency Eye Wash Station?

An emergency eye wash station is a specialized device designed to deliver a steady stream of water or saline solution to rinse the eyes immediately after exposure to harmful substances or debris. These stations are crucial in environments where chemicals are used or where there are risks of eye injuries, such as laboratories, industrial sites, and even some educational settings.
They are designed to be user-friendly and easily accessible during emergencies. Eye wash stations are equipped with quick activation mechanisms in the form of a lever, push handle, or pull rod. These require minimal force to operate, ensuring that they can be activated even by someone in distress.
Emergency eye wash stations are supplied with clean potable water ideal for decontamination. Other units contain a stored amount of saline solution treated and maintained at a quality that is safe for eye contact. A standard requirement for eye wash stations is controlled water flow and quality. Water flow, direction, and pressure are calibrated to effectively flush hazards while avoiding the possibility of exacerbating the injury.
There are several types of eye wash stations, each designed for specific environments and needs.
First, plumbed eye wash stations. These are units that are permanently connected to a water supply and are typically found in fixed locations such as chemical labs or industrial plants. Another type of emergency eyewash is the mobile or portable eye wash station. These are models that consist of a tank or storage container of flushing fluid that can be moved or transported to remote areas or locations with no direct plumbing. Lastly, there are eyewash bottle stations. These are small, handheld units filled with sterile flushing fluid, perfect for immediate use, especially when larger stations are too far away. They are often used as a first response option before reaching a plumbed or portable station.
Including emergency eye wash stations in safety protocols is not only a best practice but is often a regulatory requirement in many industries. They are a critical part of the infrastructure that helps to manage risks associated with eye injuries. Their presence can significantly mitigate the effects of accidents by providing on-the-spot decontamination, helping to prevent long-term damage, and ensuring that those exposed to hazardous materials can receive immediate help.
Factors To Consider In Integrating Emergency Eye Wash in Emergency Response
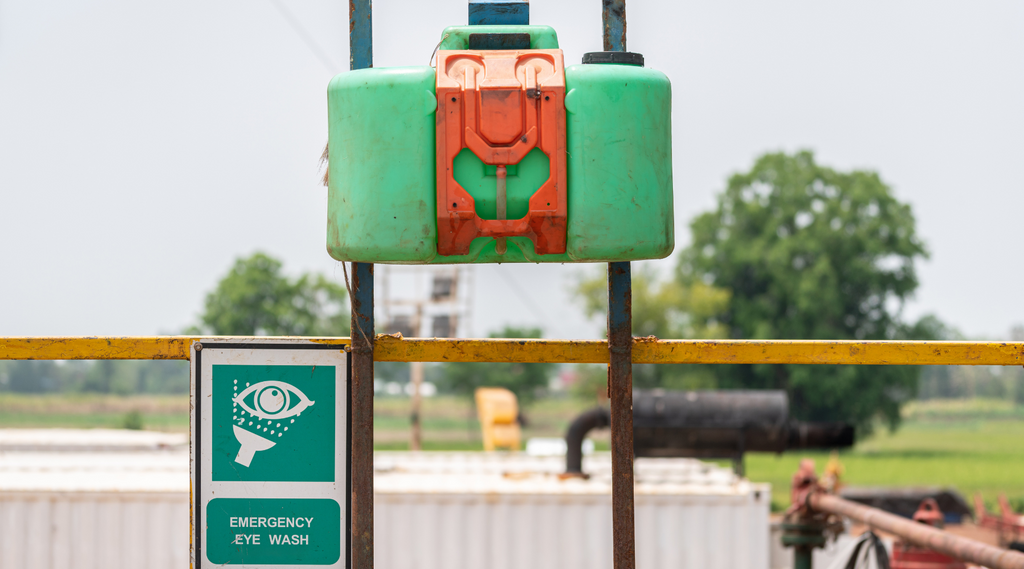
Incorporating emergency eye wash stations into disaster preparedness and emergency response plans is critical to ensuring safety, especially during natural disasters and other large-scale emergencies. This ensures that in the event of an eye injury, the response is swift and effective, minimizing the potential for long-term damage. With that, here are some factors to consider when integrating emergency eye wash stations in emergency response and preparedness plans.
Emergency Risk Assessment and Hazard Identification
Effective safety management begins with a thorough emergency risk assessment and hazard identification process. This is a critical step in ensuring that the right safety measures, like emergency eye wash stations, are in place and adequately address the specific hazards of an environment. This process is essential to effectively prepare and respond to potential hazards that can cause eye injuries.
- Understanding the Environment: The first step in the risk assessment process is a thorough understanding of the environmental and operational contexts in which eye wash stations will be used. Understanding the natural disaster risks present and specific to the location, such as flood zones, earthquake-prone areas, or regions susceptible to hurricanes. Reviewing the types of activities carried out at the site, the chemicals and materials handled, and the processes that could be disrupted during a disaster.
- Identifying Specific Hazards: This stage focuses on pinpointing the specific risks that could lead to eye injuries, such as chemical hazards, physical hazards, and secondary hazards triggered by the primary disaster.
- Assessing Vulnerability and Exposure: Once hazards are identified, the next step is to assess the vulnerability of personnel and the likelihood of exposure to these hazards during a disaster. This assessment should consider the frequency of exposure, severity of outcomes, and the population at risk.
- Implementing Risk Mitigation Strategies: Risk assessment findings inform the strategic placement and specification of eye wash stations. Placement strategy should place eye wash stations where they are most needed. In disaster-prone areas, considerations might include ensuring that stations are accessible despite possible obstructions. Furthermore, choosing between plumbed and self-contained or portable eye wash station should consider which might be more appropriate in flexible or high-risk areas.
- Continuous Monitoring and Updating: The risk assessment process is not a one-time activity but requires ongoing monitoring and adaptation as new risks emerge or as operational conditions change. Incorporate changes in operational practices, lessons learned from past incidents, and technological and regulatory updates to ensure that the emergency response plan is not only compliant but adequate to meet needs during emergencies.
Emergency risk assessment and hazard identification form the backbone of a proactive safety strategy, ensuring that emergency responders are equipped to handle potential eye injuries promptly and effectively with the help of well-placed emergency eye wash stations. The outcome should guide the placement of emergency eye wash stations—ensuring they are accessible within seconds in areas identified as high risk. It also influences the training and emergency response procedures that need to be established to address these risks effectively.
Standard and Regulatory Compliance for Emergency Eye Wash Stations
Adhering to established standards and regulations is crucial for ensuring that emergency eye wash stations are effective and safe to use in emergency situations. Compliance not only safeguards individuals from further harm during emergencies but also aligns with legal requirements that govern workplace and educational facility safety.
The Occupational Safety and Health Administration (OSHA) requires that employers provide suitable facilities for quick drenching or flushing of the eyes and body when employees are exposed to harmful chemicals. OSHA references ANSI standard Z358.1 for specific provisions related to emergency eye wash and shower equipment. Compliance with these standards is particularly important in disaster-prone areas where the risk of emergencies is heightened. Specific considerations include:
- Minimum Water Flow: Specifies the minimum flow rate for eye wash stations to ensure effective flushing of the eyes.
- Accessibility: Eye wash stations must be accessible within 10 seconds or 55 feet from the hazard, and the path must be free of obstacles.
- Installation Requirements: Units must be installed according to the manufacturer's instructions and must be modified or relocated as hazards change.
- Temperature of the Flushing Fluid: The water temperature should be tepid, generally between 60°F and 100°F, to avoid causing thermal shock or chemical interactions that could harm the eyes.
- Structural Integrity: Eye wash stations must be designed to withstand the physical conditions of a disaster, such as earthquakes or floods. This might involve additional securing measures or the installation of more robust systems that can operate effectively even after a significant disruption.
- Water Supply Reliability: In areas where natural disasters can disrupt regular water supply, alternative solutions such as portable or self-contained eye wash units should be considered. These units can provide a reliable flushing fluid supply even when main water lines are compromised.
Proper compliance ensures that when accidents happen, the risk of serious injury or long-term damage to the eyes is significantly reduced. Emergency eye wash stations that meet ANSI standards provide immediate and effective mitigation of hazards to the eyes.
Flushing Fluid Characteristics in Eye Wash Stations
The effectiveness of an emergency eye wash station greatly depends on the characteristics of the flushing fluid it dispenses. Here’s a detailed look at these critical factors:
Fluid Quality
The flushing fluid, typically sterile saline or purified water, must be free from contaminants that could exacerbate eye injuries. This requirement is crucial in disaster scenarios, where the risk of water supply contamination is increased. The fluid must mimic the natural isotonicity of human tears to avoid causing osmotic shock to the tissues of the eye, which can happen if the fluid is too dilute or too concentrated.
Fluid Duration
The duration for which the eyes must be flushed is crucial for effectively removing contaminants. ANSI Z358.1-2014 specifies that eye wash stations should provide a controlled flow of flushing fluid for a minimum of 15 minutes. This duration is considered adequate to effectively dilute and remove chemicals or foreign particles from the eyes. To meet this requirement, eye wash stations must have a sufficient supply of flushing fluid, especially in high-risk areas where more severe exposures can occur.
Fluid Pressure
The pressure at which flushing fluid is delivered must be sufficient to rinse the eyes thoroughly but gentle enough to avoid causing damage to the eyes. High pressure can exacerbate injuries by driving chemicals deeper into the eye tissues or causing mechanical damage. Eye wash stations are designed to deliver fluid gently yet effectively, usually through aerated sprays or soft-flowing nozzles to minimize the risk of injuring the eye further.
Fluid Temperature
The temperature of the flushing fluid is critical for comfort and safety. Fluid that is too cold or too hot can cause discomfort or harm, potentially discouraging individuals from using the station for the recommended duration. ANSI guidelines suggest that the flushing fluid should be tepid, generally between 60°F and 100°F. This temperature range helps to enhance the flushing effectiveness without causing thermal shock or chemical reactions that could increase the severity of the eye injury.
Fluid Contamination
Flushing fluids must be free of contamination to prevent secondary infections or additional eye injuries. Contaminated fluid can introduce new hazards to already injured eyes. Regular maintenance and inspection of eye wash stations are required to ensure the sterility and cleanliness of the fluid. For plumbed systems, this might involve periodic flushing of the system and checks for microbial contamination. Portable units need regular replacement and monitoring of the stored fluid according to manufacturer guidelines.
Emergency Personnel Training and Education
Training and education are fundamental to ensuring that emergency eye wash stations are used effectively. Knowledge of how to operate these devices promptly and properly can significantly impact the outcome of eye exposure incidents. Training ensures that all personnel are aware and understands the risks associated with the materials they handle, know the location of eye wash stations, and can operate the stations under pressure, which is critical in emergencies.
In disaster-prone areas, training should also focus on adapting to rapidly changing conditions where standard operating procedures might need to be altered. This can include training on how to access and use portable or temporary eye wash facilities if permanent stations are inaccessible. Beyond just flushing the eyes, personnel should be trained in comprehensive first aid measures that include managing eye injuries after initial flushing. This might involve training on how to recognize symptoms that require additional medical attention.
Maintenance and Inspection Requirements for Emergency Eye Wash Stations
Regular maintenance and inspection of eye wash stations are critical to ensure they operate as intended during emergencies. This includes ensuring the mechanical functionality, cleanliness, and accessibility of the stations. Well-maintained stations help prevent secondary infections caused by contaminated fluids and ensure that the mechanical parts function properly when needed.
Plumbed eye wash stations should be activated weekly to flush the system and remove any sediment or bacterial growth that could have accumulated in the pipes. This also helps ensure that the water supply is not stagnant. Portable stations, which use a stored flushing fluid, should be checked for expiration dates and sediment buildup, and the fluid should be replaced according to the manufacturer’s guidelines.
Check for leaks, clogs, or any damage to the eye wash station. Ensure that nozzles and valves operate smoothly and do not leak. Beyond visual checks, it’s important to test the operation of the eye wash station. This includes ensuring that the fluid flow starts immediately upon activation and continues at a consistent and adequate rate for a minimum of 15 minutes. After any disaster, a thorough inspection of all safety equipment, including eye wash stations, is necessary. This ensures that they are still functional and accessible, given that structural damage or changes in the environment might impact their usability.
Steps in Using Eyewash Stations in Emergency Response
When dealing with emergencies that involve hazardous substances, having access to and knowing how to properly use an emergency eye wash station can make a significant difference in minimizing eye injuries. This section covers immediate actions, proper usage, and follow-up care associated with eye wash stations during emergencies.
Immediate Action and First-Aid Response to Eye Exposure to Hazards
When hazardous materials come into contact with the eyes, immediate action is crucial to minimize damage. Quickly identify the substance involved—whether it's a chemical, physical debris, or biological agent. This will help in understanding the urgency and specific first aid measures needed.
In emergencies, time is of the essence. This is why standards state that an emergency wash station should be within 10 seconds of reach from a recognized hazardous work area. The affected individual must move to the nearest eye wash station swiftly but safely. In addition, someone should alert a supervisor or call for medical help while the injured person is using the eye wash station. The first few minutes are critical in eye injury cases.
Guide to the Proper Use of Eye Wash Stations
Using an eye wash station correctly is crucial for effective decontamination of the eyes in the event of exposure to harmful substances. Here's a more detailed look at each step involved:
- Activation of the Eye Wash Station: Ensure that the path to the eye wash station is clear and unobstructed. The station should be accessible within 10 seconds of any point where hazardous materials are handled. Eye wash stations typically have a simple mechanism to start the flow of flushing fluid, such as a push handle, pull lever, or foot pedal. This mechanism should be clearly marked and easy to operate, even by someone who is in distress.
- Proper Positioning and Eye Opening: Use your fingers to keep your eyelids open wide. In an emergency, your natural reaction might be to close your eyes tightly, but it's crucial to override this instinct to ensure thorough flushing. Position your face so that the streams of fluid flow directly onto the surface of each eye. This helps to wash away contaminants effectively.
- Duration of Flushing: The ANSI Z358.1 standard recommends flushing the eyes for at least 15 minutes. For chemical exposures, particularly those involving strong acids or alkalis, it may be necessary to flush for a longer period, depending on the substance and the extent of exposure. Do not interrupt the flushing process. Continuous flushing helps to dilute and remove contaminants and reduces the risk of serious injury.
- Techniques During Flushing: While flushing, gently move your eyeballs in all directions. This movement helps to ensure that all areas of the eyes and under the eyelids are thoroughly washed by the flushing fluid. It is critical to not rub your eyes during or after flushing, as this can cause further damage, especially if particles are involved.
- Use of Supplementary Eye Wash Options: In situations where immediate access to a plumbed or portable station isn't available, use a sterile bottled eye wash solution to begin flushing the eyes while moving towards a full-capacity eye wash station. Some facilities are equipped with combination units that include both an eye wash and a full-body shower. These units are beneficial when larger areas of the body are exposed to hazardous substances.
Follow-Up Care of Eye Injuries
After initial emergency treatment at the eye wash station, follow-up care is essential to ensure proper healing and to prevent complications:
- Medical Evaluation: Always seek professional medical evaluation after an eye injury, even if the eyes feel better post-flushing. Some chemical injuries and physical abrasions might not show immediate symptoms.
- Report the Incident: Document and report the incident according to workplace or educational facility protocols. This not only helps in further medical treatment but also contributes to preventive measures.
- Monitor Symptoms: After professional medical assessment, monitor any changes in vision, persistent pain, or signs of infection. Follow-up with medical professionals if symptoms worsen.
- Review and Reflect: Use the incident as a learning opportunity to review safety protocols and training effectiveness. This could lead to updates in procedures or additional training sessions to enhance safety.
FAQs
What is the OSHA standard for emergency eyewash?
OSHA refers to ANSI Standard Z358.1 for emergency eyewash and shower equipment, requiring that eyewash stations be accessible within 10 seconds or about 55 feet of hazardous areas, provide a controlled flow of water for a minimum of 15 minutes, and be located in an area free of obstructions.
What precautions should be taken in the use and care of eyewash stations?
Ensure regular maintenance and inspection of eyewash stations, keep the path to the stations clear, ensure all personnel know how to operate them properly, and maintain the water temperature between 60°F and 100°F to prevent discomfort or further injury.
What are the 5 basic emergency responses?
The basic responses include sounding an alarm to alert others and request help, confining hazards like fires by closing doors, evacuating the area safely via established routes, responding to the situation with available equipment and training until professional help arrives, and assisting others in exiting the area safely if possible.
What are the five things to avoid during an emergency?
During an emergency, avoid panicking to maintain clear decision-making, never ignore alarms or emergency warnings, do not use elevators especially in fires or similar situations, keep emergency exits and pathways clear at all times, and adhere to established procedures rather than improvising which can increase risks.
What are the hazards of eye wash station?
Hazards associated with eye wash stations include the risk of infection from contaminated water, potential injury from improper water temperature, mechanical failures that can prevent adequate operation, and delayed emergency response due to poorly located or obstructed stations.
What is a bump test for an eyewash station?
A bump test for an eyewash station is a quick activation of the station to ensure it functions correctly. It checks that the water flow starts immediately and that the nozzles are operational, providing assurance that the equipment is ready for use without conducting a full 15-minute test flush.